Construction productivity doesn’t fail because workers don’t show up—it fails because they show up to the wrong task, in the wrong sequence, without the right coordination. Most delays aren’t about labor shortages; they’re about poor planning. AI-powered task managers are now entering the field as quiet but relentless problem-solvers, focusing not just on task tracking but optimizing how crews are assigned, sequenced, and utilized on a daily and weekly basis.
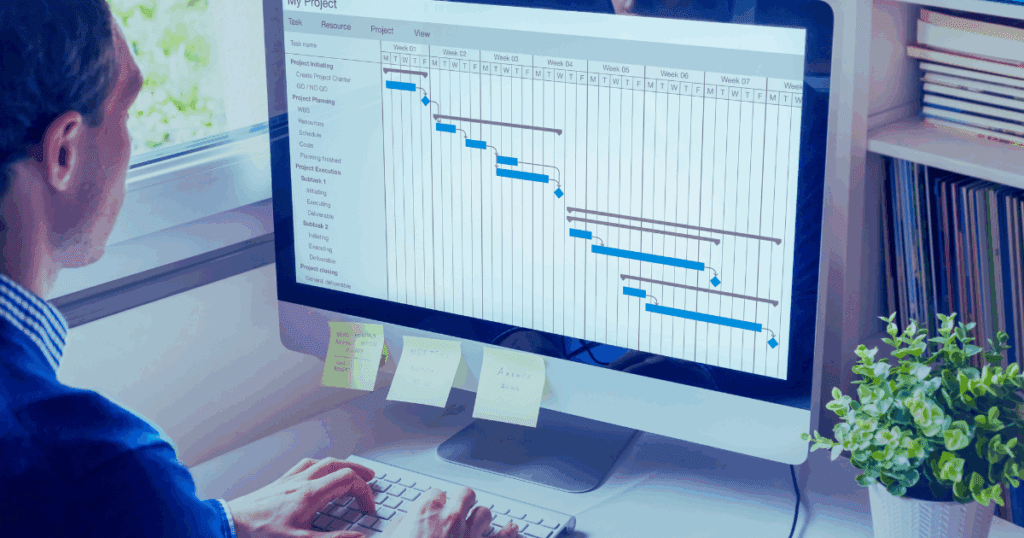
This shift is subtle. It’s not about replacing the foreman’s instinct or gut decisions. It’s about feeding them better data. AI task managers don’t hand out orders—they build context. They suggest crew allocations based on resource availability, predicted bottlenecks, weather risk, and even past performance patterns. In an industry where the schedule is written in ink but executed in dust, that kind of real-time, data-informed support changes how projects run.
The End of Static Manpower Forecasts
Ask any superintendent how they plan their manpower each week, and you’ll hear a familiar ritual: consult the master schedule, talk to trade leads, review lookaheads, then write it down. This process is manual, fluid, and frequently reworked. AI task managers are now digitizing and enhancing this layer—not by dictating who works where, but by constantly modeling how resources can be deployed more effectively based on evolving project realities.
If excavation is falling behind and steel delivery is confirmed early, the AI can simulate whether reassigning general laborers to assist with slab prep for three days will recover lost float downstream. It’s not just theoretical—these systems simulate multiple crew scenarios, rank them by schedule impact, and flag the highest-value deployments.
That doesn’t mean the superintendent follows it blindly. It means they now enter Monday morning with three options instead of one guess.
Daily Crew Tasking That Thinks Ahead
AI task managers are especially useful in short-interval planning—what needs to happen in the next 3 to 5 days to keep crews productive and on track. These platforms take inputs like current progress, weather forecasts, equipment availability, and even previous task durations to re-prioritize assignments dynamically.
Say the concrete crew finishes a pour ahead of schedule. Traditional systems would leave that as a gap until the next scheduled activity. AI task managers, on the other hand, look ahead, find tasks that can be accelerated, and suggest a reallocation—perhaps starting formwork prep for another section, or supporting a backup scope.
The system becomes a second brain for field leads. Not smarter—just faster at testing what-ifs and surfacing good calls before delays materialize.
Machine Learning Meets Trade Coordination
The construction site is a tangled web of overlapping trades, each with their own deadlines and dependencies. Coordinating them is half art, half triage. AI systems learn from past jobsite behavior—how long MEP rough-in actually takes when drywall follows too closely, or how HVAC install durations shift depending on crew size and sequence.
By analyzing historical patterns and live field data, AI task managers can flag when the planned crew mix will likely cause congestion, underutilization, or rework. They highlight trade stacking issues before boots hit the floor. This isn’t guesswork—it’s modeled off how the job is actually performing, not how it was supposed to.
This enables GCs to have more informed trade huddles. Instead of saying “We’re behind,” they can say “Drywall is tracking 1.5 days faster than expected, and we may run into HVAC delays unless their crew size increases by Thursday.”
Integration with Timecards and Field Logs
AI’s potential for crew optimization isn’t limited to planning—it extends into execution and feedback. Many AI task managers are now integrated with digital timecard systems and daily field logs. That means actual crew deployment, durations, and productivity rates are captured and fed back into the model.
If framing is consistently being completed by a 3-person crew in 6 hours instead of the estimated 8, the system learns. It begins to adjust future projections, recommending similar resourcing for similar scopes elsewhere. Over time, the estimate vs. actual gap narrows—not because estimators changed their templates, but because the AI is closing the loop in real time.
This cycle turns raw labor data into something more valuable: learning. Not in a static database, but in a constantly improving model that fine-tunes every week’s plan with the precision of hindsight.
Predictive Fatigue and Overloading Alerts
Crew optimization isn’t just about efficiency—it’s also about sustainability. AI task managers now factor in labor fatigue, sequence intensity, and even rest periods. If a plumbing crew has been working high-output tasks for six days straight, the system might recommend a low-intensity task shift or even a rotation to reduce burnout and prevent safety incidents.
By using time-on-task data, task complexity, and environmental stressors like temperature or confined space, these systems issue alerts when crew loads become unbalanced or potentially hazardous. For the field manager, that’s not micromanagement—it’s a silent assistant checking the blind spots.
And when safety and productivity align, the system proves its value not just in numbers but in trust.
Hyper-Local Adjustments Based on Field Realities
Weather, deliveries, and unexpected delays don’t show up in Gantt charts—but they do happen on job sites every day. AI task managers are designed to absorb that variability without derailing the plan.
If a materials delay is logged into the project system or a weather API flags a storm, the AI can immediately reroute planned crews to alternate tasks, avoiding lost time. The best systems don’t just reschedule—they reprioritize based on actual productivity impact. Some even recommend partial crew splitting, allowing a foreman to assign half their team to scaffold prep while the other half begins layout elsewhere.
The output isn’t a new Gantt chart. It’s a decision framework for the person on the ground. That’s where productivity planning becomes truly responsive.
Crew-Level Transparency Without Micromanaging
In traditional systems, productivity was something reviewed weekly, often after it was too late to act. AI task managers now give real-time visibility into how each crew is performing against plan. But instead of focusing on individual workers, they focus on task outcomes, sequence adherence, and forecast drift.
This allows superintendents and PMs to spot trends early—crews consistently completing certain scopes ahead or behind plan, or tasks that always require more hands than estimated. It’s not surveillance. It’s insight. Delivered without bias, enabling better planning conversations without the guesswork or finger-pointing.
Also Read:
Safety First: Enhancing Toolbox Talks with AI-Powered Safety Management in Ezelogs
Smart HR for Construction: Boosting Payroll Efficiency with Ezelogs’ AI-Enabled HRM Tools
Compliance Made Easy: How AI-Enabled Certified Payroll in Ezelogs Simplifies Regulatory Reporting
Centralizing Your Data: The Power of Ezelogs’ Product Data Sheet Library for Faster Submittals
Voice-Activated Efficiency: Transforming Construction Management with Ezelogs’