In construction, delays don’t just cost time—they cost money. A single setback can trigger a domino effect, pushing back critical tasks, increasing labor costs, and throwing budgets into disarray.
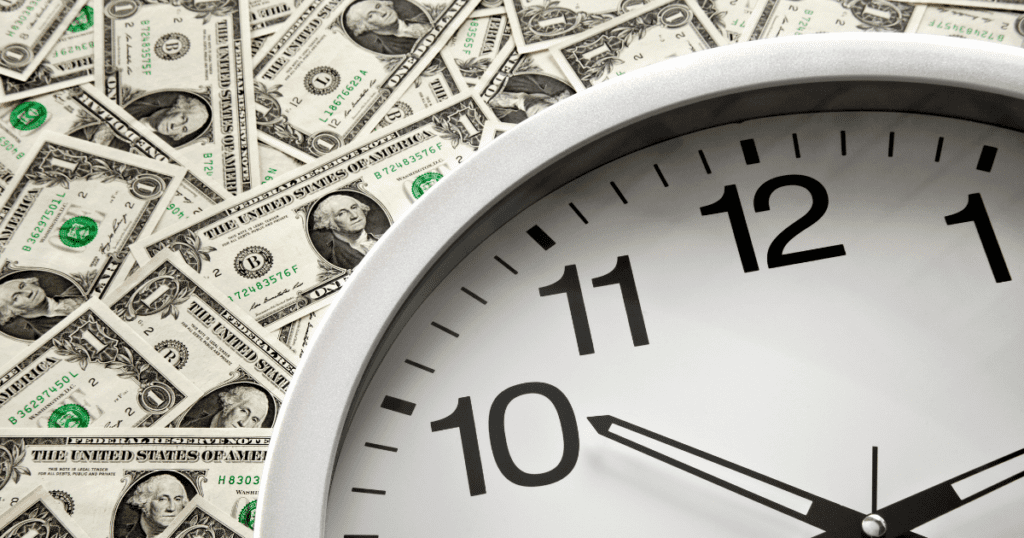
Traditional scheduling methods, often reliant on static Gantt charts and gut instinct, struggle to keep pace with the unpredictable nature of job sites. Enter smart scheduling algorithms: the silent force behind on-time and on-budget projects.
The Problem with Conventional Scheduling
Construction schedules have long been built around fixed sequences, assuming ideal conditions. But weather changes, material delays, and workforce fluctuations rarely adhere to a neatly laid-out timeline. Project managers spend countless hours adjusting plans manually, trying to mitigate conflicts as they arise.
Manual Scheduling Pitfalls
- Rigid Dependencies: A delay in one phase ripples across the project, but traditional scheduling doesn’t adapt in real time.
- Human Error: Managers make decisions based on limited data, often underestimating risks.
- Lack of Real-Time Insights: By the time an issue is identified, it’s often too late to prevent the impact.
Smart scheduling algorithms address these issues by continuously analyzing variables and adjusting plans dynamically.
How Smart Scheduling Algorithms Work
At the core of these algorithms is artificial intelligence (AI) and machine learning (ML). They process vast amounts of data—worker availability, material delivery schedules, weather forecasts, historical project data—and generate schedules optimized for efficiency.
Real-Time Adaptation
Unlike static scheduling, smart algorithms constantly recalculate timelines based on real-time data. If heavy rain is forecasted, exterior work is rescheduled while indoor tasks are prioritized, preventing unnecessary downtime.
Resource Synchronization
By analyzing the movement of materials and equipment, smart scheduling ensures that workers aren’t waiting around for supplies or tools to arrive. If a shipment is delayed, affected tasks are automatically rescheduled, preventing cascading delays.
Optimizing Labor Efficiency
Dynamic Workforce Allocation
A project’s labor requirements shift daily, and overstaffing or understaffing can be costly. Smart scheduling balances workloads by predicting labor demand and redistributing workers accordingly. If a framing crew finishes early, the algorithm identifies where their skills are needed next, reducing idle time.
Predicting Labor Shortages Before They Happen
By analyzing past attendance patterns, weather conditions, and external factors, these algorithms anticipate labor shortages before they become critical. If a shortage is expected, automated notifications prompt managers to adjust staffing levels in advance.
Preventing Equipment Bottlenecks
Smart Allocation of Machinery
Cranes, bulldozers, and other equipment are expensive to rent, and inefficient scheduling can lead to underutilization or conflicts. Scheduling algorithms optimize usage by assigning machines based on priority needs, ensuring they are always in use but never double-booked.
Reducing Idle Time
If an excavator is scheduled for two different tasks at the same time, the system flags the conflict and reorganizes the work order to maximize efficiency. This ensures that costly equipment isn’t sitting idle while crews wait.
Weather-Responsive Scheduling
Mitigating Weather-Related Delays
Smart scheduling integrates real-time weather data to prevent disruptions. If high winds make crane operations unsafe, the algorithm reassigns workers to alternative tasks, avoiding unnecessary stoppages.
Seasonal Adjustments
For long-term projects, historical weather data helps refine scheduling. If a region experiences frequent snowfall in January, critical outdoor tasks are scheduled earlier, preventing winter shutdowns.
Keeping Supply Chains Aligned
Material Arrival Coordination
One of the biggest causes of delays is material unavailability. Smart scheduling links directly with suppliers, adjusting the construction timeline based on real-time shipping data. If a delivery is postponed, non-dependent tasks are prioritized to keep the project moving.
Minimizing Storage Costs
Over-ordering materials leads to storage challenges, while under-ordering results in delays. Algorithms predict exactly how much material is needed at each stage, ensuring optimal inventory levels on-site.
Proactive Conflict Resolution
Automated Risk Detection
Smart scheduling doesn’t just react to delays—it prevents them. By analyzing past project data, these systems identify patterns that could lead to future conflicts. If a subcontractor has a history of delays, the algorithm factors this into the schedule, building in contingencies.
Scenario Simulation
Before making scheduling changes, project managers can run “what-if” simulations. If a key supplier goes out of business, or if a major task runs over by a week, the system tests multiple solutions to find the least disruptive option.
Smarter Scheduling for Smoother Projects
Time lost is money lost, and construction projects no longer have to rely on outdated scheduling methods. Smart scheduling algorithms ensure every resource—human, material, and mechanical—is allocated at the right time and place. With AI-driven adjustments, projects stay on track, budgets remain intact, and efficiency becomes the new standard.
Also Read:
EzeLogs Quantum: Revolutionizing Construction Levelling
Maximizing Efficiency with BIM VDC: A Guide for Construction Professionals
Quantum Solutions for Construction Project Management
Why BIM Programs are Essential for Modern Construction Projects
Smart Construction: Quantum Scheduling & Resource Planning
Enhancing Risk Mitigation Tracking in Construction Projects