The construction industry has long struggled with project delays and budget overruns. Traditional project management methods, while effective in many ways, often fail to account for unforeseen risks and inefficiencies that can disrupt schedules and inflate costs.
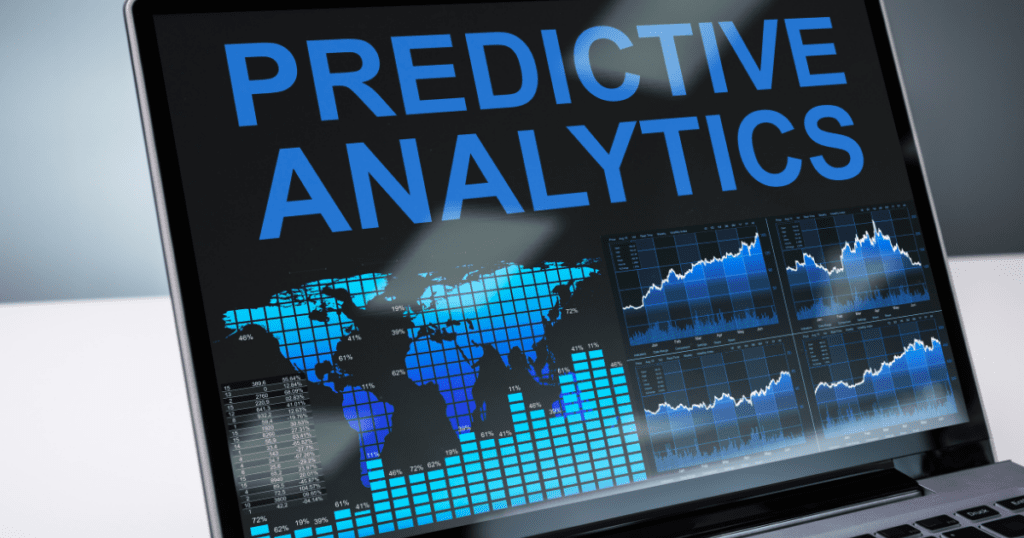
Predictive analytics is emerging as a critical solution to these challenges, offering data-driven insights that enable proactive decision-making. By leveraging historical data, real-time monitoring, and advanced algorithms, construction firms can mitigate potential risks, optimize workflows, and enhance overall project efficiency.
Identifying Risk Factors Before They Escalate
Construction projects are highly complex, involving multiple variables such as labor availability, material supply chains, weather conditions, and regulatory compliance. Each of these factors carries inherent risks that can derail progress if not properly managed. Predictive analytics helps project managers identify early warning signs of potential disruptions by analyzing past project data and recognizing patterns that indicate trouble.
Machine learning models assess key performance indicators (KPIs) such as subcontractor reliability, equipment usage, and site productivity to flag risks before they become major issues. For instance, if historical data suggests that a specific supplier frequently delivers materials late, predictive analytics can alert project managers to secure alternative vendors in advance, preventing costly delays.
Additionally, AI-driven predictive models analyze weather patterns to anticipate conditions that might impact construction timelines. If a project is scheduled during a season prone to heavy rainfall, predictive analytics can suggest contingency plans, such as adjusting work schedules or using weather-resistant materials. This proactive approach minimizes disruptions and keeps projects on track.
Optimizing Resource Allocation
One of the most significant contributors to construction delays is inefficient resource allocation. Traditional scheduling methods often rely on estimates and manual planning, leading to misallocation of labor and materials. Predictive analytics transforms this process by dynamically adjusting resource deployment based on real-time data and historical trends.
By analyzing workforce productivity, predictive models determine the optimal distribution of labor across various project phases. If a particular task is taking longer than anticipated, predictive analytics can recommend shifting personnel from less critical activities to accelerate progress. Similarly, by tracking equipment usage and maintenance records, project managers can anticipate potential machinery breakdowns and schedule preventive maintenance, reducing unexpected downtime.
Material procurement is another area where predictive analytics drives efficiency. By evaluating supplier performance and demand fluctuations, predictive models ensure that materials arrive precisely when needed, avoiding both shortages and excess inventory. This just-in-time approach reduces waste, controls costs, and maintains steady workflow continuity.
Enhancing Cost Control and Budget Accuracy
Cost overruns remain one of the biggest challenges in construction, often caused by poor planning, scope changes, and unforeseen expenses. Predictive analytics significantly improves budget accuracy by analyzing historical financial data and identifying cost patterns that contribute to overruns.
Advanced forecasting models assess various project components—such as labor costs, material expenses, and equipment rental rates—to provide a more precise estimate of the total budget required. These insights help construction firms develop more realistic financial plans, reducing the likelihood of unexpected expenses derailing a project.
Moreover, predictive analytics enhances contract management by detecting potential budget deviations early. If a subcontractor’s cost projections exceed the original estimate, predictive models flag discrepancies and allow project managers to renegotiate terms or explore alternative vendors before the budget spirals out of control.
By continuously monitoring project expenditures and comparing them against projected costs, predictive analytics ensures that financial risks are identified and mitigated before they escalate. This level of financial oversight keeps construction projects within budget and reduces the reliance on costly emergency funding.
Improving Scheduling and Timeline Accuracy
Project schedules are often disrupted due to unforeseen delays, miscommunication, and inefficient task sequencing. Traditional scheduling tools provide static timelines that do not account for real-time changes in site conditions. Predictive analytics revolutionizes scheduling by using dynamic modeling to adjust timelines based on evolving project circumstances.
By analyzing workflow dependencies and task durations, predictive models identify potential bottlenecks and suggest alternative sequencing to maintain progress. If a specific phase is delayed, predictive analytics can propose parallel workstreams to offset lost time and prevent cascading delays across the project.
Real-time data integration further enhances scheduling accuracy. Site sensors, IoT devices, and worker tracking systems feed live data into predictive models, ensuring that schedules are continuously updated to reflect actual progress. This dynamic scheduling approach enables project managers to make data-driven adjustments in real time, keeping timelines intact.
Enhancing Quality Control and Defect Prevention
Rework due to construction defects is a major cause of delays and cost overruns. Traditional quality control methods rely on manual inspections, which are often time-consuming and prone to human error. Predictive analytics enhances quality assurance by analyzing past defect patterns and identifying areas most susceptible to errors.
AI-powered image recognition and sensor-based monitoring detect deviations in structural integrity, material composition, and construction techniques. These insights enable teams to address potential defects before they compromise project quality.
Additionally, predictive analytics helps enforce compliance with industry standards and safety regulations. By analyzing inspection records and regulatory guidelines, predictive models flag potential compliance issues early, reducing the risk of costly legal disputes and project shutdowns.
Strengthening Supply Chain Resilience
The construction industry heavily depends on supply chains for materials, equipment, and workforce coordination. Supply chain disruptions—whether due to geopolitical events, economic fluctuations, or logistical bottlenecks—can significantly impact project timelines and costs. Predictive analytics strengthens supply chain resilience by forecasting disruptions and recommending mitigation strategies.
By analyzing global supply chain trends, predictive models anticipate material shortages and price fluctuations, allowing construction firms to secure materials in advance at optimal costs. Additionally, predictive analytics assesses supplier reliability, identifying vendors with consistent delivery performance and minimizing dependency on high-risk suppliers.
For transportation logistics, predictive analytics optimizes delivery routes and schedules by accounting for factors such as traffic conditions, fuel costs, and warehouse availability. This ensures that materials and equipment reach construction sites on time, preventing delays caused by logistical inefficiencies.
Integrating Predictive Analytics with Construction Technologies
The full potential of predictive analytics is realized when integrated with other construction technologies, such as BIM, IoT, and AI-driven project management platforms.
BIM integration allows predictive analytics to simulate project scenarios, assess risk factors, and generate optimized construction plans. IoT devices provide real-time data on equipment performance, worker productivity, and environmental conditions, enhancing the accuracy of predictive models.
AI-driven project management platforms leverage predictive analytics to provide automated recommendations, helping project managers make data-driven decisions with greater confidence. The seamless interaction between these technologies creates a data-driven ecosystem that continuously enhances construction efficiency and mitigates potential disruptions.
Predictive analytics is reshaping the construction industry by transforming how projects are planned, executed, and managed. By leveraging historical data, real-time monitoring, and advanced forecasting techniques, construction firms can prevent delays, control costs, and improve overall efficiency. The integration of predictive analytics with modern construction technologies ensures that projects are not only completed on time and within budget but also meet the highest standards of quality and safety.
Also Read:
EzeLogs Quantum: Revolutionizing Construction Levelling
Maximizing Efficiency with BIM VDC: A Guide for Construction Professionals
Quantum Solutions for Construction Project Management
Why BIM Programs are Essential for Modern Construction Projects
Smart Construction: Quantum Scheduling & Resource Planning
Enhancing Risk Mitigation Tracking in Construction Projects