A robotic arm moves with precision, layering concrete with an almost hypnotic rhythm. No hammers, no scaffolding—just a machine executing a digital blueprint with meticulous accuracy.
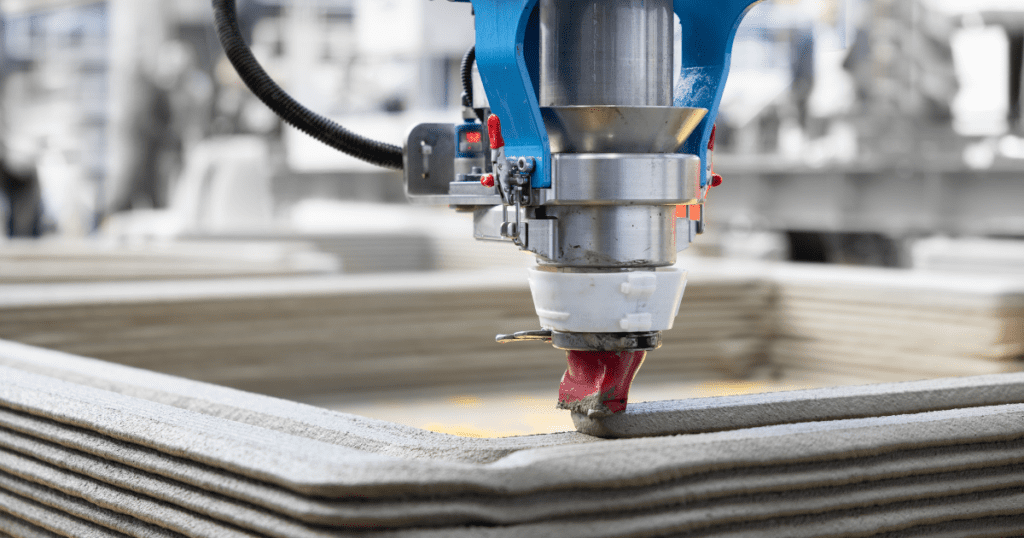
What once seemed like a futuristic fantasy is now unfolding on construction sites worldwide. 3D printing is no longer confined to prototypes; it’s actively shaping how buildings, bridges, and entire communities come to life.
From Scale Models to Full-Scale Structures
The Shift from Planning Tools to Real-World Construction
Architects and engineers have long relied on scaled models to visualize designs before breaking ground. Traditionally, these models were painstakingly assembled by hand—cutting, gluing, and refining small pieces to represent a much larger vision. Then came 3D printing.
With digital fabrication, intricate models can be produced in hours, not days. Layer by layer, printers transform raw materials into highly detailed structures, allowing teams to analyze form, function, and feasibility with unprecedented precision. But while these printed models were initially tools for planning, it wasn’t long before the industry asked: why stop at scale models?
Material Science and the Leap to Full-Scale Printing
The leap from miniature prototypes to full-scale construction wasn’t instantaneous, but pioneers saw potential. If a printer could create a detailed model, what was stopping it from printing walls, floors, or entire buildings? Advances in material science answered that question. Concrete, polymer composites, and even recycled materials became viable printing mediums. As the technology matured, what once existed only in concept sketches began rising as tangible structures.
Rethinking Construction Speed and Cost
How 3D Printing Accelerates the Build Process
Speed has always been a driving factor in construction. A standard residential building can take months—or even years—to complete, factoring in labor, weather delays, and material availability. 3D printing introduces a different equation.
Instead of waiting for traditional crews to lay bricks, frame walls, and pour concrete, large-scale 3D printers can build entire structures in days. Automated extrusion systems deposit layers of material according to a precise digital design, eliminating the inefficiencies of human error and material waste.
A prime example is the growing use of printed concrete homes. In some regions, housing shortages demand rapid solutions. A 3D-printed house, fully functional and ready for occupancy, can be built in under 48 hours. Labor costs drop dramatically, material waste is minimized, and affordability becomes a realistic goal rather than an abstract ideal.
The Cost Benefits of Digital Fabrication
For developers, this shift isn’t just about speed—it’s about rethinking cost structures. Traditional construction involves multiple subcontractors, equipment rentals, and supply chain logistics. With 3D printing, many of these variables shrink. Fewer workers are needed on-site, and the process consumes only the material required for the print—no excess, no unnecessary cuts, and no hauling away of wasted materials.
Pushing the Limits of Design
Breaking Free from Traditional Architectural Constraints
Beyond efficiency, 3D printing challenges the very notion of architectural constraints. Traditional construction methods rely on formwork, molds, and rigid materials. Curves, organic shapes, and intricate facades require extensive manual labor and additional costs. But what happens when a printer doesn’t care whether it’s building a straight wall or a sweeping archway?
Suddenly, design flexibility expands. Architects can experiment with complex geometries that would be impractical with conventional techniques. Parametric design—where algorithms generate intricate, structurally sound forms—becomes a practical reality. Unique facades, self-supporting domes, and biomimetic structures take shape with the same ease as a basic square room.
Engineering Marvels: Printed Bridges and Beyond
This newfound freedom is particularly evident in experimental projects like printed bridges. In the Netherlands, engineers unveiled the world’s first 3D-printed steel bridge, demonstrating how the technology can tackle projects that would have been prohibitively expensive using standard methods. Without traditional welding or casting, the bridge took shape in a controlled printing process, layer by layer.
Revolutionizing Sustainability in Construction
Reducing Waste and Maximizing Resource Efficiency
The construction industry is responsible for nearly 40% of global carbon emissions, much of it tied to material production and transportation. 3D printing disrupts this cycle by reducing waste and optimizing resource use.
Traditional building methods generate excess material—cut-off wood, unused bricks, spilled concrete. With additive manufacturing, construction becomes precise. Materials are deposited exactly where needed, reducing excess. Some projects are even experimenting with repurposed construction waste, using recycled concrete mixtures as printing material.
Energy Efficiency and Smart Construction Materials
Beyond waste reduction, energy efficiency plays a role. Structures designed through parametric modeling can be optimized for insulation, airflow, and natural light. Some printed buildings incorporate built-in voids for insulation, reducing the need for additional energy-intensive modifications post-construction.
Challenges and the Road Ahead
Overcoming Material and Regulatory Limitations
Despite its promise, 3D printing in construction isn’t without hurdles. Material limitations remain a key challenge—while concrete printing is advancing, other construction essentials like plumbing, electrical systems, and insulation still require human installation. Regulatory codes, largely written for conventional methods, often struggle to accommodate printed structures, slowing adoption.
Scaling Up for Widespread Adoption
Even with these roadblocks, progress continues. Research labs and startups push boundaries daily, refining techniques and exploring new materials. Governments and investors take notice, funding initiatives aimed at scaling up this technology. The shift from prototype to project is no longer a question of possibility—it’s a matter of how soon the industry fully embraces it.
Also Read:
EzeLogs Quantum: Revolutionizing Construction Levelling
Maximizing Efficiency with BIM VDC: A Guide for Construction Professionals
Quantum Solutions for Construction Project Management
Why BIM Programs are Essential for Modern Construction Projects
Smart Construction: Quantum Scheduling & Resource Planning
Enhancing Risk Mitigation Tracking in Construction Projects