Construction projects are complex, multifaceted undertakings where risk is ever-present. From unexpected delays to safety hazards, financial strains, and changing regulations, risks in construction projects can arise at any stage.
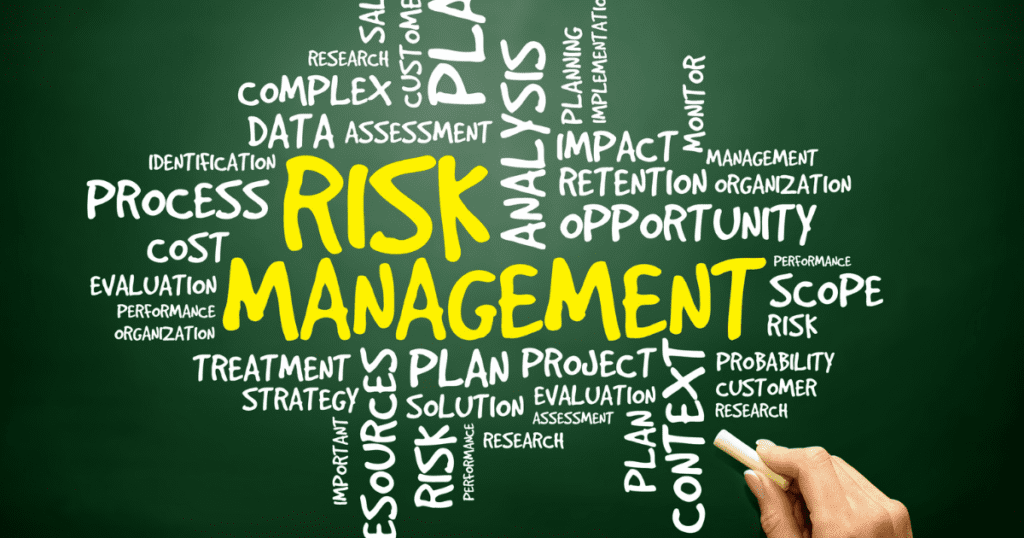
Traditional risk control approaches—contingency planning, safety measures, and insurance policies—have served the industry for years. However, the rise of technology and more sophisticated management methods has brought forward advanced strategies that provide more proactive, data-driven, and collaborative approaches to mitigating risk. These advanced strategies are changing the way construction projects are managed, enabling teams to anticipate, respond to, and control risks effectively from start to finish.
Also Read: Guide to Construction Risk Assessment Techniques
Risk Identification and Assessment: Going Beyond the Obvious
The first step in risk management is identifying potential risks. In construction, this involves understanding the challenges that could impact the project’s timeline, budget, or safety. Traditionally, risk identification may focus on common issues like weather delays, material shortages, or labor shortages. However, with more advanced strategies, the scope of risk assessment expands beyond the obvious.
Data-Driven Risk Mapping
Modern construction management uses data analytics tools to enhance risk identification. Analyzing historical data from similar past projects can help project managers predict potential risks with a higher degree of accuracy. Predictive analytics models assess variables such as weather patterns, supply chain disruptions, or labor trends, enabling managers to anticipate issues before they materialize. For instance, if certain regions face seasonal weather risks, managers can prepare their schedules and resources accordingly to avoid potential delays due to storms.
Also Read: Comprehensive Guide to Construction Risk Assessment Techniques
Proactive Risk Mitigation: Using Technology to Stay Ahead
Once risks are identified, mitigation is key. Traditional methods like setting aside contingency funds or adding buffer times to schedules remain important, but modern technology has taken risk mitigation to the next level, making it more proactive rather than reactive.
Building Information Modeling (BIM)
One of the most significant advancements in proactive risk mitigation is Building Information Modeling (BIM). BIM is a digital representation of the project, integrating information from design, construction, and operations into a 3D model. It allows teams to visualize the entire project before physical work begins, helping to identify potential issues early on. For example, clashes between electrical systems and plumbing can be detected in the digital model, avoiding delays and costly changes during construction. BIM also allows managers to simulate different construction workflows, optimizing the process to avoid bottlenecks or errors.
Drones and Real-Time Monitoring
Another technology improving risk mitigation is drones. Drones provide real-time data on the progress and safety conditions of the job site. With aerial footage, drones can identify safety hazards, track materials, or monitor site logistics without the need for manual inspection. This continuous flow of real-time information enables project managers to react quickly to changing conditions. For example, if a safety risk is identified, the team can immediately intervene, preventing accidents or delays.
Also Read: Why BIM Programs are Essential for Modern Construction Projects
Collaborative Risk Management: Engaging All Stakeholders
Risk management doesn’t belong to just the project manager or contractor. A collaborative approach involving all stakeholders—designers, subcontractors, suppliers, and clients—ensures that potential risks are understood from all angles, creating a holistic strategy to minimize those risks.
Cloud-Based Collaboration Platforms
Cloud-based tools like Procore, Buildertrend, and CoConstruct enable seamless communication between all project stakeholders. These platforms allow real-time sharing of project data, including updated schedules, budgets, and risk assessments. When all stakeholders have access to the same data, they can promptly identify potential risks and adjust their plans accordingly. For example, if a subcontractor faces delays, the project manager can notify the entire team, allowing the project to adjust and stay on track.
Risk Workshops and Team-Based Planning
Engaging in risk workshops or brainstorming sessions early in the project can help stakeholders identify risks from multiple perspectives. For instance, during design meetings, architects may be aware of structural risks, while contractors may flag issues related to site access or resource procurement. By bringing together all relevant parties, project managers can ensure that all risks are acknowledged and addressed before they become significant issues.
Real-Time Risk Tracking: Staying Agile with Adaptable Strategies
No matter how well-planned a construction project may be, risks will inevitably emerge during the execution phase. Advanced risk management strategies now include tools and systems to track risks in real-time, allowing project managers to adapt and adjust swiftly.
Internet of Things (IoT) and Wearables
IoT technology and wearable devices are changing the way construction managers track risks in real-time. IoT sensors can be embedded in equipment, materials, and even worker uniforms to monitor conditions continuously. For example, equipment can send alerts when it’s nearing the end of its operational lifespan, allowing for timely maintenance or replacement. Wearables on workers can track vital signs like heart rate or body temperature, alerting supervisors to early signs of fatigue or heat-related illnesses before they result in accidents.
Predictive Analytics and Machine Learning
Predictive analytics and machine learning offer powerful tools for identifying potential risks before they occur. These technologies analyze large sets of data from both the current project and past projects, identifying patterns that may indicate future risks. For example, predictive models can forecast project delays based on supply chain issues or changing regulations, helping project managers take corrective action before these risks impact the schedule or budget. By continuously learning from new data, these tools improve their predictive capabilities, providing managers with up-to-date information on potential risks.
Also Read: Maximizing Efficiency with BIM VDC: A Guide for Construction Professionals
Financial Risk Control: Integrating Risk Management with Budgeting
Financial risk is a major concern in construction, and advanced risk control strategies now link financial management directly with risk management to anticipate and manage cost overruns or unforeseen expenses.
Advanced Budgeting Tools and Cost Forecasting
Advanced project management tools now offer real-time cost forecasting capabilities that link budgets with schedules and project timelines. This integration allows project managers to identify potential financial risks early. For example, if material costs increase unexpectedly, managers can quickly adjust the project budget or shift resources to avoid overruns. By combining financial data with real-time project progress, construction managers can anticipate risks related to funding, labor costs, and material prices more accurately than ever before.
Risk-Adjusted Budgeting
In advanced risk management, budgets are not fixed; they are risk-adjusted. This means that construction managers create budgets that incorporate potential risks identified during the project’s lifecycle. Instead of relying on standard contingency funds, these budgets take a more dynamic approach, adjusting as risks materialize or change. If a supply chain disruption occurs, the project’s budget can be adjusted to accommodate additional costs, ensuring that the project stays financially viable without compromising on key objectives.
The Role of Technology in Advanced Risk Control
The integration of technology in advanced risk control strategies is undeniable. Tools such as BIM, drones, IoT sensors, and predictive analytics have redefined how construction projects approach risk. By using data to make proactive decisions, managing risks collaboratively with stakeholders, and continuously tracking risks in real time, construction managers are better equipped to navigate the complexities of modern construction projects.
The ability to predict, identify, and respond to risks with precision and speed has a significant impact on project timelines, costs, and safety. As technology continues to evolve, it is likely that these strategies will become even more refined, offering even greater opportunities for risk control in construction management.