Construction quality management has always been a high-stakes operation, balancing time pressures, subcontractor coordination, material specifications, and inspection cycles. But even with the best intentions, QA/QC workflows often unravel under the weight of paperwork, manual checklists, and misaligned approvals. A missing inspection photo or unchecked line item can lead to rework, failed handoffs, or warranty claims.
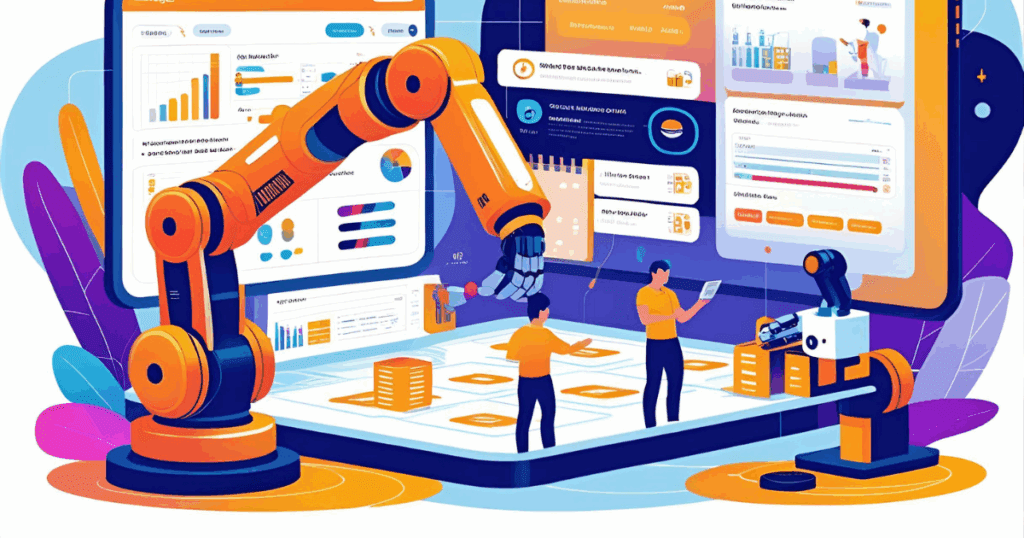
Ezelogs is redefining this landscape with AI-powered quality management tools that don’t just digitize inspections—they learn from them. The platform embeds intelligent QA/QC into daily workflows, integrating field activity, specification data, inspection criteria, and real-time alerts. This system doesn’t require teams to adopt new behavior—it reinforces best practices by automating accountability and detecting quality drift before it turns into rework.
Contextual Checklists that Think Like a Superintendent
Traditional QA/QC checklists are static forms—pre-filled templates that rarely reflect real-time project dynamics. Ezelogs replaces this with dynamic, AI-generated checklists that adapt to specific trades, locations, and project phases.
When a framing crew logs completion of wall assemblies on Level 3, the system triggers the corresponding inspection checklist based on trade scope, spec section, and historical QC data. If the system knows that a specific subcontractor has previously had fastener spacing issues, it adds a verification step automatically. If the project has enhanced seismic requirements, those are embedded into every relevant checklist.
This approach eliminates one-size-fits-all forms. Each checklist is built from a live matrix of CSI divisions, submittal data, jurisdictional requirements, and past inspection results. It knows what to ask, when to ask, and who needs to verify.
AI-Assisted Image Recognition for Visual Confirmation
Field quality control often comes down to documentation—photos of completed work, screenshots of test meters, or videos of assemblies under stress. But those media files are rarely organized or audited. Ezelogs integrates AI image recognition that reviews uploaded photos and verifies that key elements are captured.
If a checklist item requires rebar placement with correct bar spacing and cover, the AI scans the image for compliance. If a concrete pour photo is uploaded without evidence of slump test equipment or formwork alignment, the system flags it. Over time, it learns which inspectors over-document or under-document, and adjusts prompts accordingly.
This eliminates the guesswork of whether photo documentation is sufficient. It also protects contractors from future disputes by timestamping and geotagging verified quality visuals.
Specification Alignment at the Point of Inspection
Quality failures often arise from a disconnect between what’s installed and what’s specified. Ezelogs connects QA/QC tasks directly to the spec book. When a quality checklist is generated, it includes embedded reference to the relevant spec section, submittal approvals, and material data.
If the inspection is for fireproofing, the AI loads the approved submittal, thickness tolerances, and application method directly into the inspector’s tablet or phone. No more flipping through binders or relying on memory. Any deviation between the installed product and approved specs triggers an alert, prompting re-inspection or documentation of variance approval.
This level of alignment ensures that what’s being verified is the right thing, applied in the right context, with the right reference backing it.
Real-Time Punch List Creation and Auto-Sync
As inspections are conducted, deficiencies are flagged in real time and instantly populate the project’s punch list. There’s no lag between inspection and punch creation, and no need for a coordinator to transcribe paper notes into a log.
Each punch item is tagged by location, trade, and spec section. If a door frame is misaligned or missing fasteners, the responsible subcontractor is notified with the specific location, required fix, and photographic evidence. Once fixed, the item is closed with AI-verification (image comparison, checklist match, or re-inspection trigger).
This punch workflow is continuous—not a last-week rush before TCO. It builds project quality progressively, reducing the punch backlog and ensuring accountability from the start.
Predictive Deficiency Detection and Risk Scoring
The AI engine inside Ezelogs does more than checklist routing—it learns from historical jobsite behavior. If a subcontractor has a high incidence of repeated issues, or if a specific activity (e.g., waterproofing) consistently triggers punch items across projects, the system elevates the risk profile of similar activities moving forward.
These predictive signals are tied to phase planning. If the system sees that five previous jobs had window flashing issues in phases 4–6, it adds extra inspection steps, prompts early material review, and increases the frequency of site walks during that period.
This transforms QA/QC from a reactive to a proactive function. Project managers can see a heatmap of where risk is likely to emerge—before it costs time or damages client confidence.
Closeout Packages Built from Verified Quality Logs
One of the most painful parts of construction closeout is assembling documentation to prove quality standards were met. Ezelogs builds this package as the project runs—not after. Every checklist, inspection photo, approved variance, and test result is auto-logged, sorted by spec section and building zone.
At the time of closeout, AI assembles a compliance-verified quality binder ready for handoff. For public or regulated projects, this includes stamped checklists, time-stamped image logs, inspection signatures, and linked submittals. No file digging. No retroactive uploads. Just a clean, automated proof of quality.
The system also tracks which items required rework, what caused it, and how long it took to resolve—data that feeds back into estimating, scheduling, and subcontractor evaluations for future work.
Crew-Level QA Accountability and Skill Feedback
Beyond inspections, Ezelogs tracks who performed what work, and how their output fared under inspection. If a specific crew consistently installs drywall with no punch items and fast inspections, that crew is tagged with a high-quality rating. Conversely, if another crew generates repeat deficiencies in MEP rough-in, the system flags this to the foreman and recommends additional oversight.
Over time, this builds a data-rich profile of crew strengths, weaknesses, and training opportunities. Quality management isn’t just about catching errors—it becomes part of workforce development, subcontractor rating, and project forecasting.
Also Read:
Digital Twin + AI for Lifecycle Optimization & Decision-Making
Quantum Computing & AI for Advanced Construction Planning
Smart HR for Construction: Boosting Payroll Efficiency with Ezelogs’ AI-Enabled HRM Tools
AR/VR Integration with AI for Quantity Takeoff & Site Planning
Centralizing Your Data: The Power of Ezelogs’ Product Data Sheet Library for Faster Submittals
Voice-Activated Efficiency: Transforming Construction Management with Ezelogs’